top of page
designing your own iPhone case

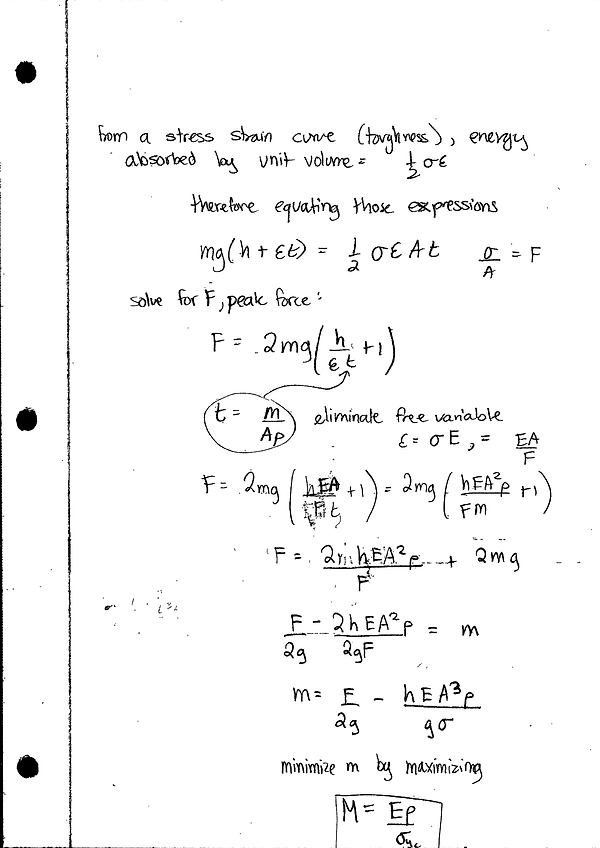
Ashby Charts as produced by CES Selector to maximize M


Manufacturing Process Selection
Currently, phone cases are mainly made in China and Taiwan. Hard plastic cases are manufactured from either polycarbonate, hard polyurethane or polypropylene, and soft plastic covers are made up of regular polyurethane or thermoplastic polyurethane. These cases are made with injection molding. Machine for this is custom-designed with a mold base crafted from several chromium steel bars. Plastic is poured into the injection mold which has attained the desired design and it is cooled and hardened.[1]
sources
1. http://mobilecaseshq.com/how-different-material-mobile-phone-covers-are-manufactured/
Our Cases
for prototyping, what is most convenient for us is to use the Jacobs Hall Carbon 3D Printer to print on polyurethane, which is included in the family of appropriate materials by the materials index. However, how about for scale up?
We assumed iphone case made up of elastomer with mass around 30 g, thickness around 1mm, tolerance less than 0.1 mm, roughness less than 1 μm and economic batch size around 10000.
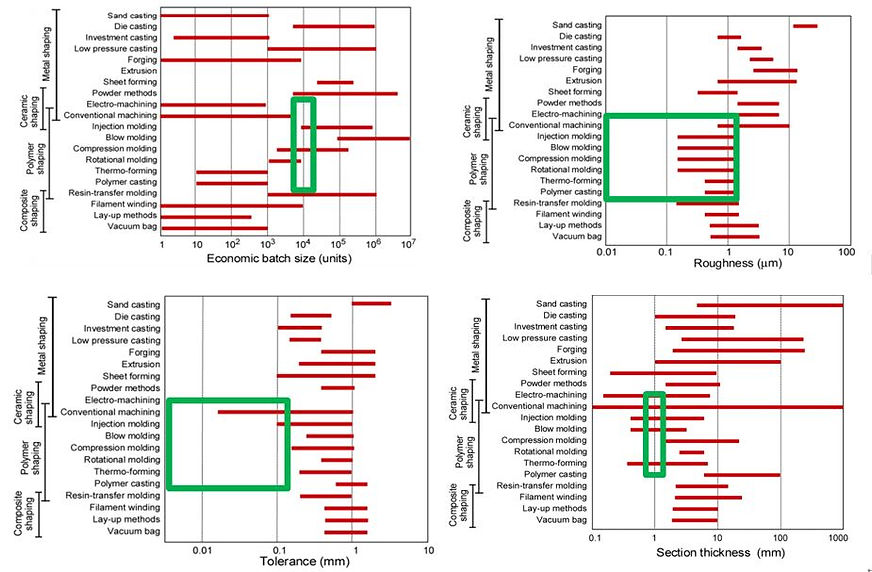


Based on the charts above, we determine the appropriate manufacturing techniques, which are copied below:
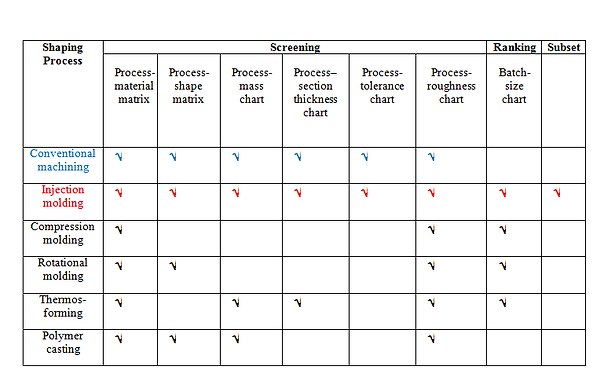
Therefore, our primary process which meets all design constraints would be injection molding and secondary process would be conventional machining.
source of the charts:
http://www.grantadesign.com/download/pdf/teaching_resource_books/2-Materials-Charts-2010.pdf
For the cases themselves, which have standardized ports, those may be manufactured by injection molding as well, while the accessories are laser cut or 3D printed, depending on the user's preference.
bottom of page